Typical automotive plastic injection moulds include dashboards, headlights, door panels, instrument clusters and more. Manufacturers use injection molding for a number of different reasons, from the flexibility of the process to the wide variety of plastic materials available.Injection molding is a reliable manufacturing method for generating solid plastic parts. The process consists of injecting molten plastic material into a mold cavity, cooling it, and extracting the finished part.
Auto plastic moulding is a very important component in the automotive industry and offers many advantages over metal stamping. These include a high level of quality, cost-effective production, and compatibility with a variety of different polymers.Plastic components are often lighter than their metal counterparts, which makes them ideal for improving fuel efficiency without sacrificing power. This helps meet the demands of consumers for eco-friendly vehicles and government regulations requiring higher fuel-efficiency levels.
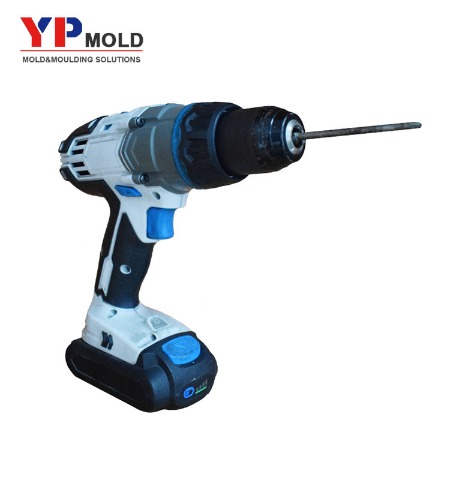
In addition to being lightweight, plastic components can also be easily modified for specific color schemes. For example, manufacturers can mix dyes with the raw materials and then inject them into a molded plastic piece to create solid, consistent colors that match the vehicle’s color scheme.Injection molding is a complex and demanding manufacturing process that requires a well-designed mold. In order to ensure that a molded plastic product is of optimal quality, a quality control team carries out rigorous inspections from raw material through the finished part. This includes dimensional and structural checks. Depending on the complexity of a molded component, the quality control team may need to run checks at different times during production.