Hot runner mould is a plastic injection molding system that eliminates the need for a cold runner. This reduces production and material costs while reducing cycle time.
The runner that runs from the injection nozzle to the part is heated and liquefied during the process, which allows it to run straight through the mold cavity without any limitation. This runner is then ejected and separated from the finished product, recycled and reground into a pool of raw materials that can be used for future cycles.
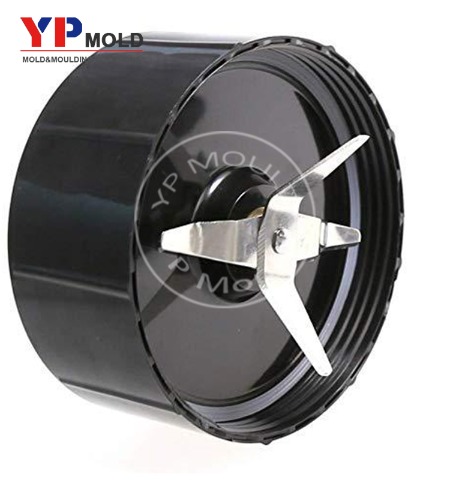
Another advantage of hot runner system is that it uses the same plastic raw materials that are being molded, which minimizes waste and ensures consistent quality and performance. This also decreases labor, and increases productivity.
There are two types of hot runner systems: externally and internally heated. The former has annulus flow passages that are heated by a probe and torpedo located in the passages. This method is a good option for thick-walled parts where heat retention and control are critical.
Both insulated and internal-heated runners offer significant benefits to molders. Insulated runners have extra-large runner channels that keep the molten flow path open during continuous cycling. This system is an inexpensive solution for molds that need to accommodate color changes and easy part removal.
Both insulated and internal-heated runners use a temperature controller to maintain a constant temperature throughout the mold. This temperature controller can help to eliminate issues associated with cycle interruption, such as overheating and degradation of the mold or the plastic part. It can also track the onset of overheating during the process and automatically lower the temperature to eradicate it.