The injection moulding process is an important part of manufacturing plastic products. During this operation, plastic is injected under high pressure into a mold cavity. After the plastic material is injected, it cools and hardens inside the mould. Afterwards, it is ejected from the mould.A good plastic injection mould design includes complex geometries and features such as undercuts. It is important to incorporate an effective cooling system to ensure the proper cooling of the molten plastic.
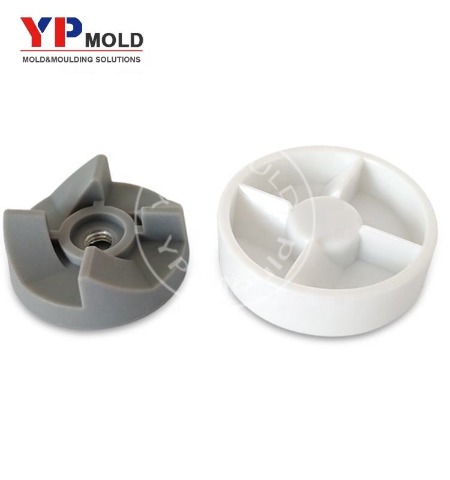
A well-constructed plastic injection mould can help to reduce production costs, while providing quality parts. Some important parameters to consider when choosing an injection mould include the material, cost of resin, and the amount of plastic needed.Another aspect to consider is the size of the injection mould. Injection moulds can be designed to create single or multiple cavities. This can vary by product. For example, a two-shot mould is used to combine different materials for additional colour.
Molds can also be made from aluminum or steel. Aluminium moulds have lower mechanical and dimensional tolerances than steel ones. However, they are not ideal for use in high volume production or applications with tight dimensional tolerances.Typically, injection molds are constructed in two halves. The front, or fixed part of the mould, is a platen that is closed during the injection process. The movable part is then closed and the halves are separated.Once the halves are separated, the molten plastic is injected into the cavity of the mould. The pressure from the injection system helps the plastic to compact into the mould.