Plastic moulds are used in a variety of industries, including automotive, home appliances, and toys. In addition to being durable and easy to work with, they are also inexpensive.The main plastic moulding processes are injection molding, blow moulding, compression moulding, and rotomoulding. These techniques allow for rapid production of large volumes of plastic parts.Plastic injection moulding is the most common technique for producing appliance parts. This method uses high-pressure injections, allowing the plastic to reach deep into the mold. After the plastic has been injected into the mould, it is cooled to retain its shape.
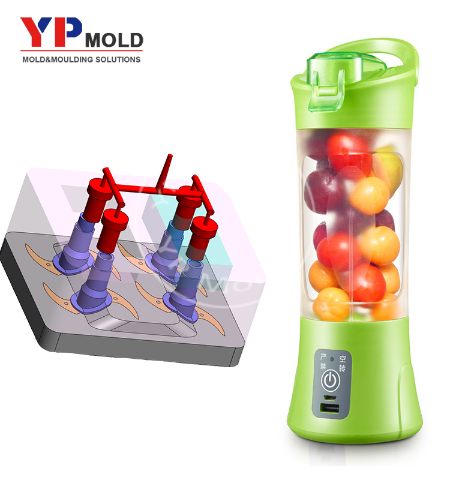
The use of injection moulding allows for customization of the design of the plastic parts. Its low cost and ease of remolding means that it is highly popular in the home appliance industry. A number of household appliances, from dishwashers to blender containers, use this technique.Another important benefit of using injection molding is that it helps to minimize the need for additional processing after the mould has been molded. As a result, the cost of manufacturing a large number of appliances is reduced.
Home appliances made from plastic components are also more corrosion-resistant and can last 70 percent longer than a comparable metal part. They are also cheaper, which results in quicker product completion.Plastic moulding is a vital component of our daily lives. Whether we use it for making toys for our children, or for making health care supplies, plastic is a critical element of our lives.