Plastic injection moulding is a manufacturing process that creates complex parts from plastic. It is used in mass production, including the automobile industry and the electronics industry.There are several steps in the process of injection molding. First, a sprue is formed. This is a passageway for the molten plastic to enter the mould cavity. The sprue is then connected to a runner system. Each runner has a gate on the end.
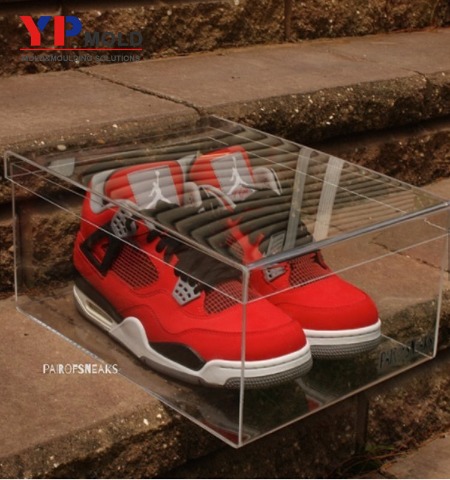
A plunger or screw is used to apply pressure on the sprue. As molten plastic flows through the sprue, the pressure is reduced. Once the sprue and runner have passed the gate, the molten plastic is then injected into the mould cavity.During the cooling stage, a coolant is used to reduce the heat of the molten plastic. In addition, an air vent is built to eliminate trapped gases. These features help eliminate the occurrence of distortion and poor surface finish.
After the part has cooled, ejectors are used to remove the finished product. Proper mould maintenance is crucial to the life of the mould. Ejection difficulties can cause interruptions to the production cycle.When the plastic material has reached a solid state, excess materials will adhere to the part. Trimming will then be used to separate the molded units.The sprue picker is a robotic device that allows the mold to be pre-staged before it is pressed into use. Besides reducing the amount of action time in and out of the mold, the sprue picker is also capable of placing the sprues in a granulator for recycling.